Glass plays an essential role in medical equipment — especially inside X-ray detectors.
These medical devices require a specialized glass composition to ensure the material withstands extreme heat and energy, as well as repeated applications of radiation technology.
In addition to high levels of heat and light, the glass in X-ray equipment must also offer the following properties:
- Endurance to high transition temperatures.
- Low thermal expansion to maintain dimensions under the stress of construction and operation.
- Pristine surface quality and flatness for the best quality images and highest accuracy.
BOROFLOAT® Glass: An Excellent Choice for Medical Applications
Of the many glass options available for medical devices, BOROFLOAT® glass is one of the best choices. While general glass absorbs radiation and deteriorates, BOROFLOAT® glass is not easily changed by high-energy radiation, and is therefore not as susceptible to darkening, as seen in the photo below.
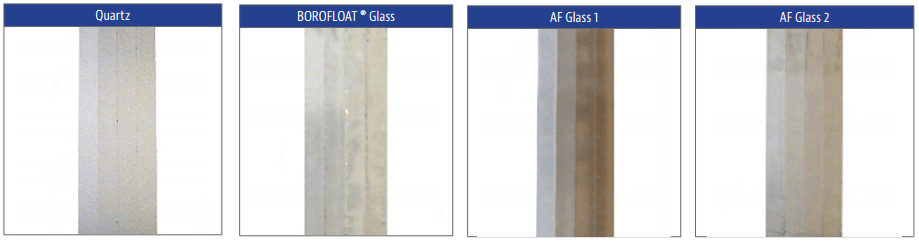
BOROFLOAT® glass is also extremely versatile, and can serve as a scintillator substrate, cover slip, protective window for X-ray rooms, and many other related applications.
Learn More Today
At Swift Glass, our customers in the medical device industry count on us for fabrication to their specification. We partnered with BOROFLOAT® glass manufacturer SCHOTT to put together an educational white paper, BOROFLOAT® Glass in the Medical Industry: How It Resists Radiation’s Effects.
This technical guide further explains the unique construction of BOROFLOAT® glass and its sizes, thicknesses, and tolerances in which it is available.

Take a look at our guide today, and please contact us directly if you have any questions or would like a quote.
3D printing, also called additive manufacturing, is rapidly transforming industrial manufacturing as we know it.
Initially used to create models and prototypes, 3D printing is now increasingly being used to construct finished products.
In the near future, this technology will hold the power to manufacture food, cars, implants, and even soft tissue organs.
The 3D printing process uses computer-automated layering of material to create a three-dimensional object. Just about any material available in liquid or powder form can be 3D printed. The industrial robots performing the layering can be programmed with complex shapes and geometries to produce a diverse range of parts with extreme precision and detail.
Where Does Glass Fit In?
During the 3D printing process, the object being created requires a platform on which to rest. Because of the high temperatures experienced during 3D printing, this plate must be made from durable, heat-resistant materials.
Borosilicate – a glass substance constituted of silica and boron oxide – is the material of choice for these applications. An extremely low coefficient of thermal expansion makes borosilicate more resistant to thermal shock than any other common glass. Even when exposed to high temperatures (up to 500°F or 260° C), borosilicate remains durable and clear without losing functionality.
Get More Information from Swift Glass
Swift Glass has been a worldwide leader in custom glass fabrication for almost 100 years. In addition to waterjet cutting, glass tempering, polishing, grinding, lapping, and drilling services, we offer a variety of borosilicate and infrared reflecting borosilicate (IRR) glass from major manufacturers such as Corning and Schott.
For more information about Swift Glass and our offering of glass for 3D printing, please visit our borosilicate materials page. You can also check out our latest eBook about strengthened glass called Creating Glass That Withstands Extreme Environments.